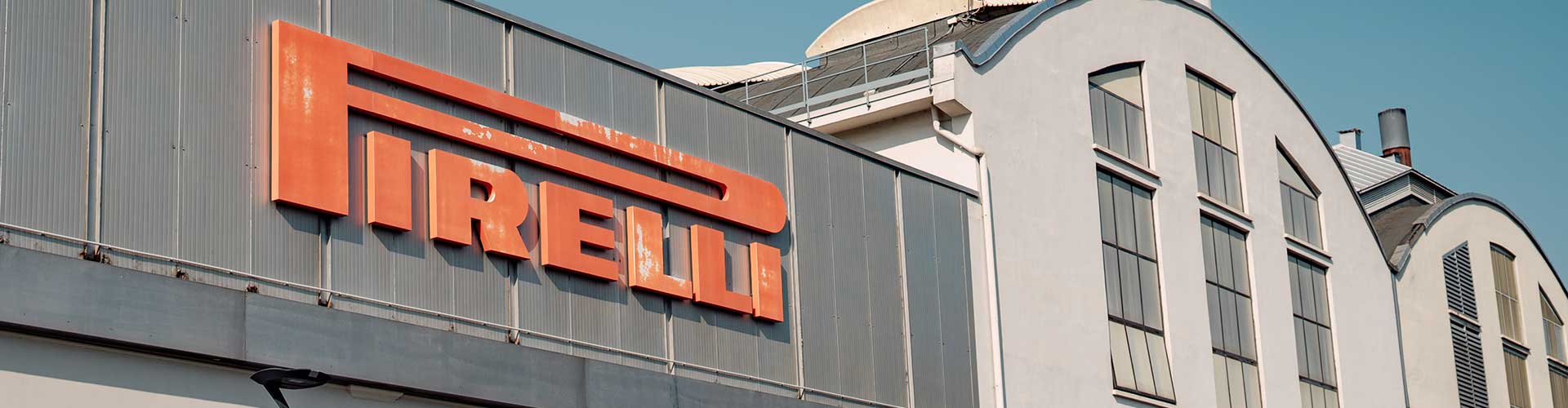
Pirelli Bicycle Tyres
Behind the Scenes
When renowned tyre manufacturer Pirelli stepped back into the world of cycling in 2017, it piqued a lot of interest. Suddenly, one of the giants of modern motorsport was bringing their expertise to the pro peloton and beyond. You don’t develop a Formula 1 tyre without a massive understanding of performance, precision and marginal gains. We visited the Pirelli research and development facility in Milan with the promise that their bike tyres are no afterthought. What we found, however, is that they’re a key part of a holistic obsession.
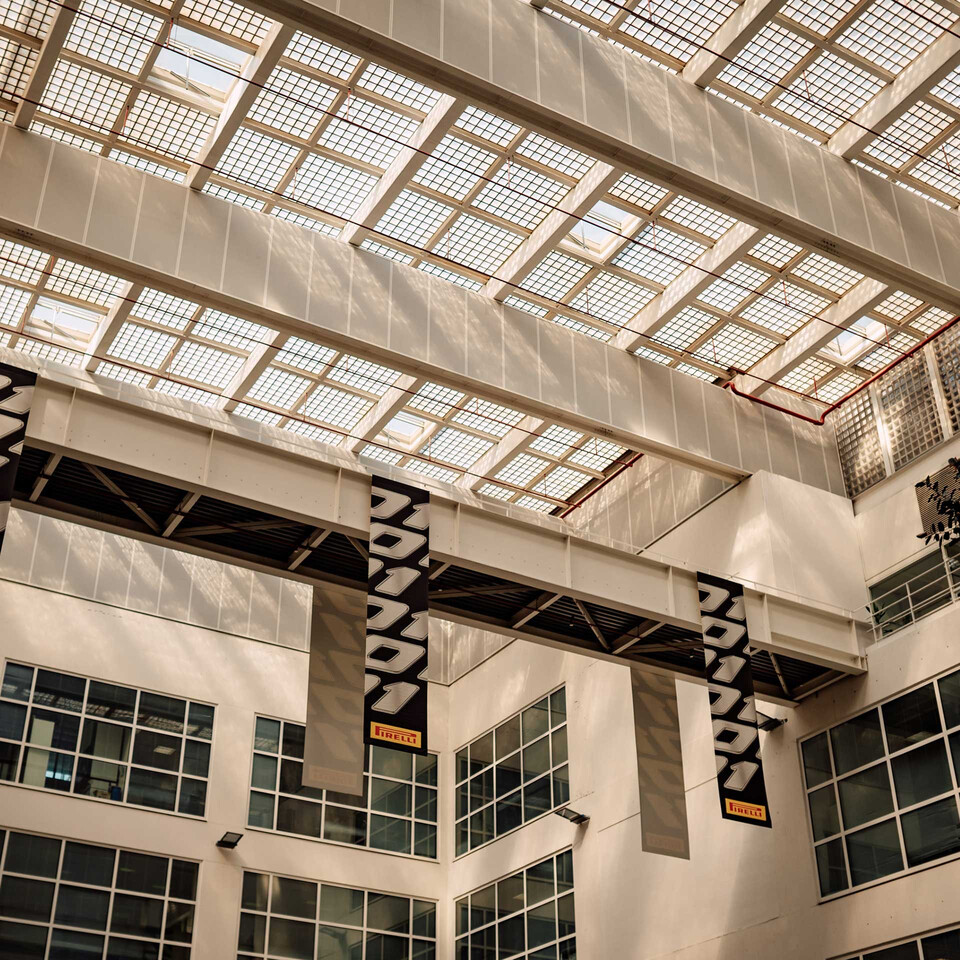
The P ZERO Laboratory
The development process of Pirelli’s product range is so specialist, that they have an entire five-storey building solely dedicated to R&D. It's here where the P ZERO™ line is developed and refined. Perhaps most famously used in Formula 1 motor racing, it’s the same committed research and development team that delivers performance tyres to all platforms, from sports cars and trucks to motorcycles and bicycles.
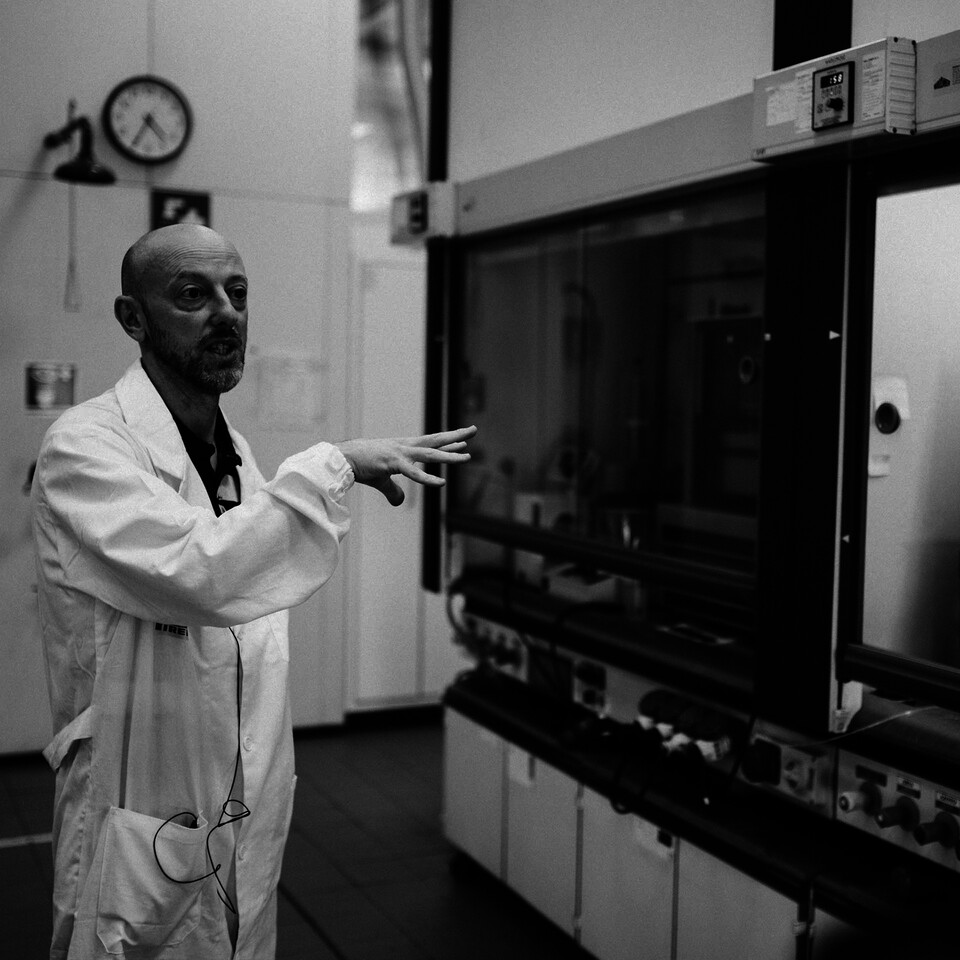
P ZERO Chemistry Lab
This is research and development at a level that can only be described as obsessive. The process begins at a molecular level in the Chemistry Lab, where Marco Colombo had a keen ability to explain complicated technical processes in plain English - such as how the process of vulcanisation essentially turns chewing gum into elastic. We felt like we were in the presence of the tyre industry’s Walter White, a virtuoso in compounding who detailed the roles of fillers, vulcanisers, protective agents, accelerants and materials like aramid to keep construction light, or metallic wire for reinforcing.
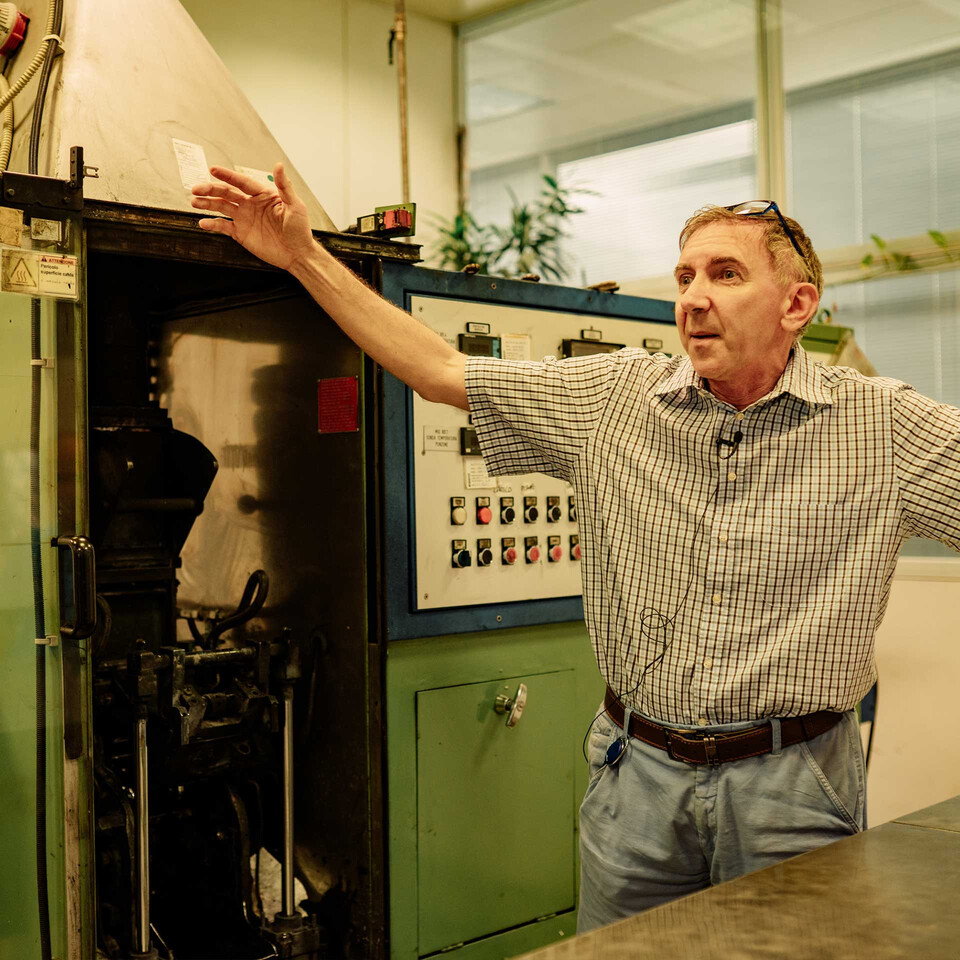
P ZERO Physics Lab
If we’d just met Heisenberg, then at the Physics Lab, we were about to be introduced to Pirelli’s Mary Berry. Paolo Massimino is an animated and passionate professional, who charmingly explained how the ‘cooking process’ is just as important as the ‘recipe’. Up to 16,000 rubber compounds are formulated each year, and they all need production and testing.
Using scaled down versions of factory machines, they can create small disc-shaped samples of compounds quickly and efficiently. By testing attributes such as hardness, elongation, compression or elasticity, the team can almost instantly determine if the sample has achieved its aims. In real terms, these goals might be anything from improved puncture protection, additional suppleness or better UV protection for longevity, to name but a few. The variations between compounds can be microscopic in their differences, but this is a company striving for perfection.
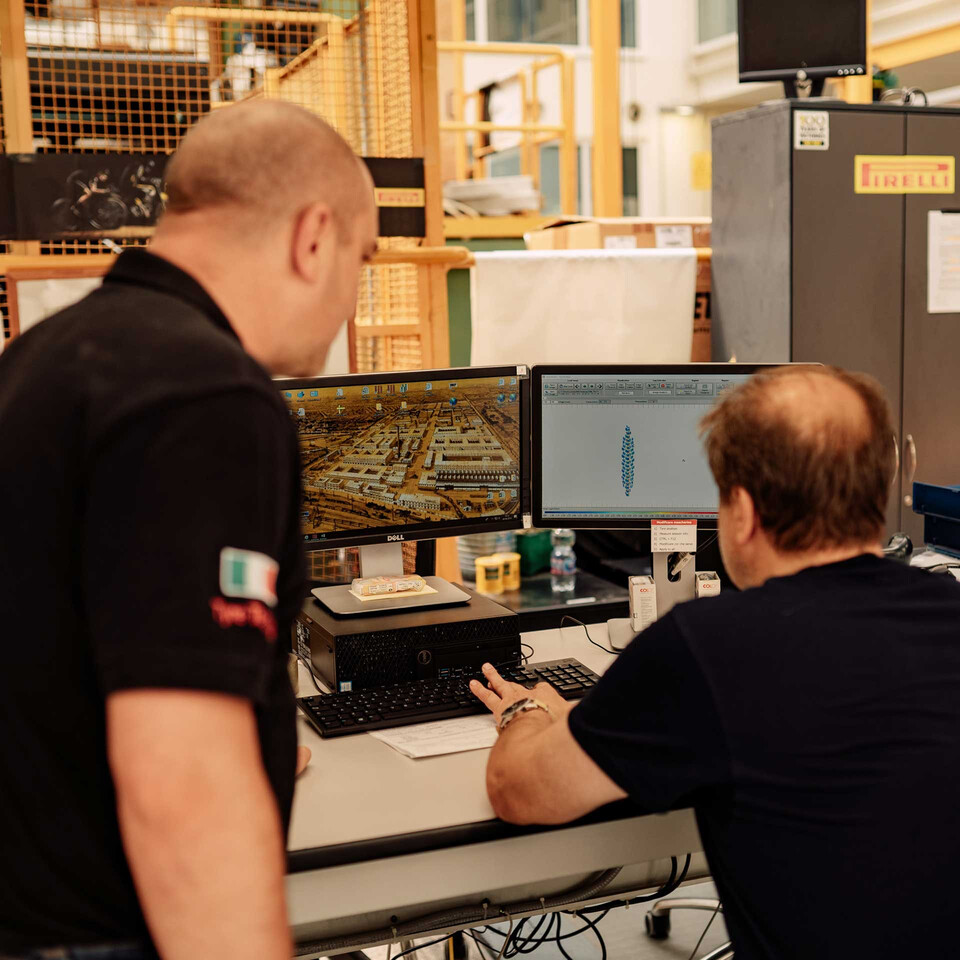
Laboratory Testing
The bottom two floors of the P ZERO™ building are dedicated to testing these new products. Not only do they put their own tyres through stringent tests, they also benchmark against their leading competitors across all disciplines.
Static tests check prototype tyre performance in a stationary, controlled environment. Lasers are used for precision measurements on tyres when new, and after thousands of kilometres. When industry standards and stock sensors aren’t accurate enough, Pirelli develops their own, such is their dedication to getting things right.
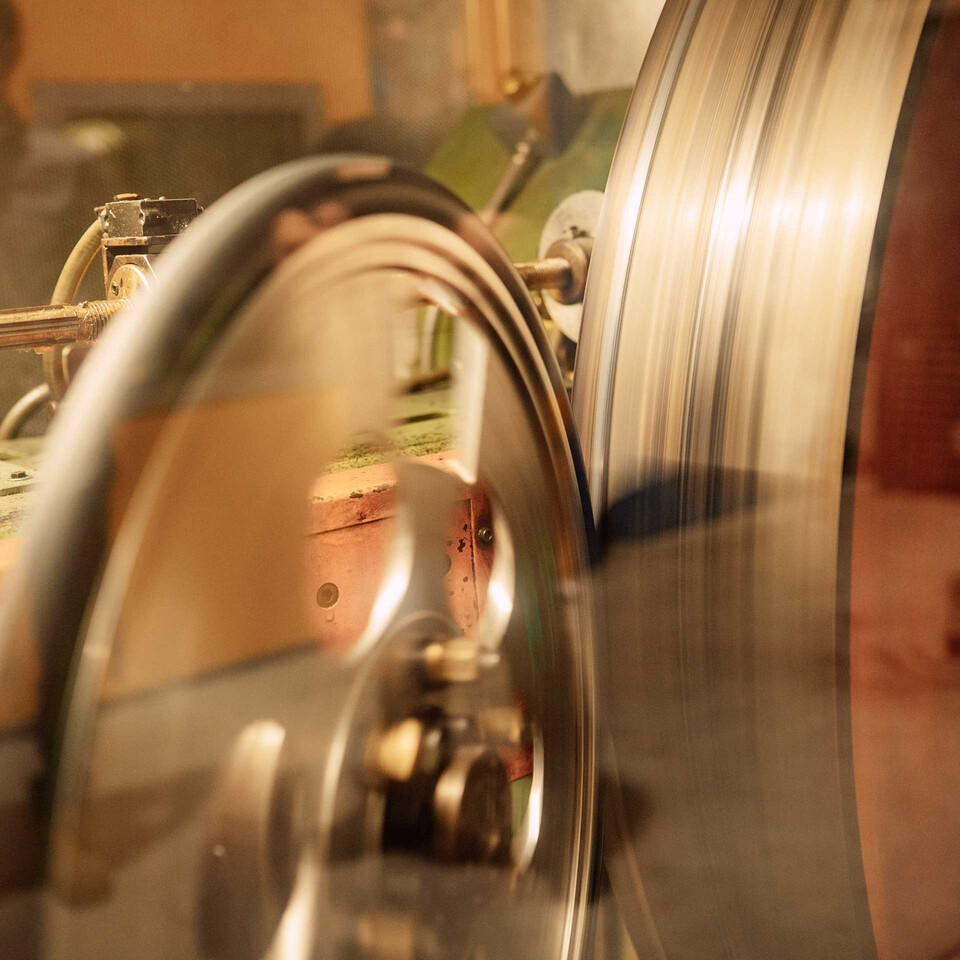
The Dynamic Testing facilities include a room on suspension, which hosts a conveyor belt to better match the surface of a road. Since the belt is flat, it provides a more accurate contact area than the curve of a rolling road. This method can be time-consuming and expensive, but Pirelli looks first at accuracy in its tests.
Standard rolling drum tests are performed here too, checking rolling resistance and tyre wear on both textured and smooth surfaces. A bike tyre has to endure thousands of kilometres at 50km/h in a test like this. They test the casing too, by rolling the tyre on the drum with tilt angles hardly achievable by a human.
Testing is not limited to the Pirelli Laboratory, however, as independent testing from the Polytechnic in Milan is used to verify results, as well as real-world performance at the company’s impressive test track facility.
Real World Dynamic Testing

Soon, it’s apparent that the obsession for perfection and the scientific ethos is consistent across the Pirelli organisation. For instance, test driver Alessandro Pileri informs us that the pristine tarmac was relaid in the past year, but was allowed to bed-in for four months before testing could resume. This was in order to best replicate the attributes of an average European tarmac road. A constant layer of surface water is kept uniform at a chosen depth between 3-9mm by an advanced sprinkler system. This is the track where all Pirelli tyres are tested for performance in wet conditions, and everything is heavily regulated.
The range of tests includes a wet circuit with a wide radius high-speed turn as well as shorter, sharper corners and a bridge that helps replicate a short downhill section. There's a former runway finished in a variety of surfaces, including tarmac, concrete and two kinds of cobbles, which is used for braking and noise tests for all vehicles. When testing vehicles in wet conditions, they use milk to clearly identify the footprint of the tyres. ISO test certified, this needs to be scientifically accurate and repeatable, and so it's taken very seriously.
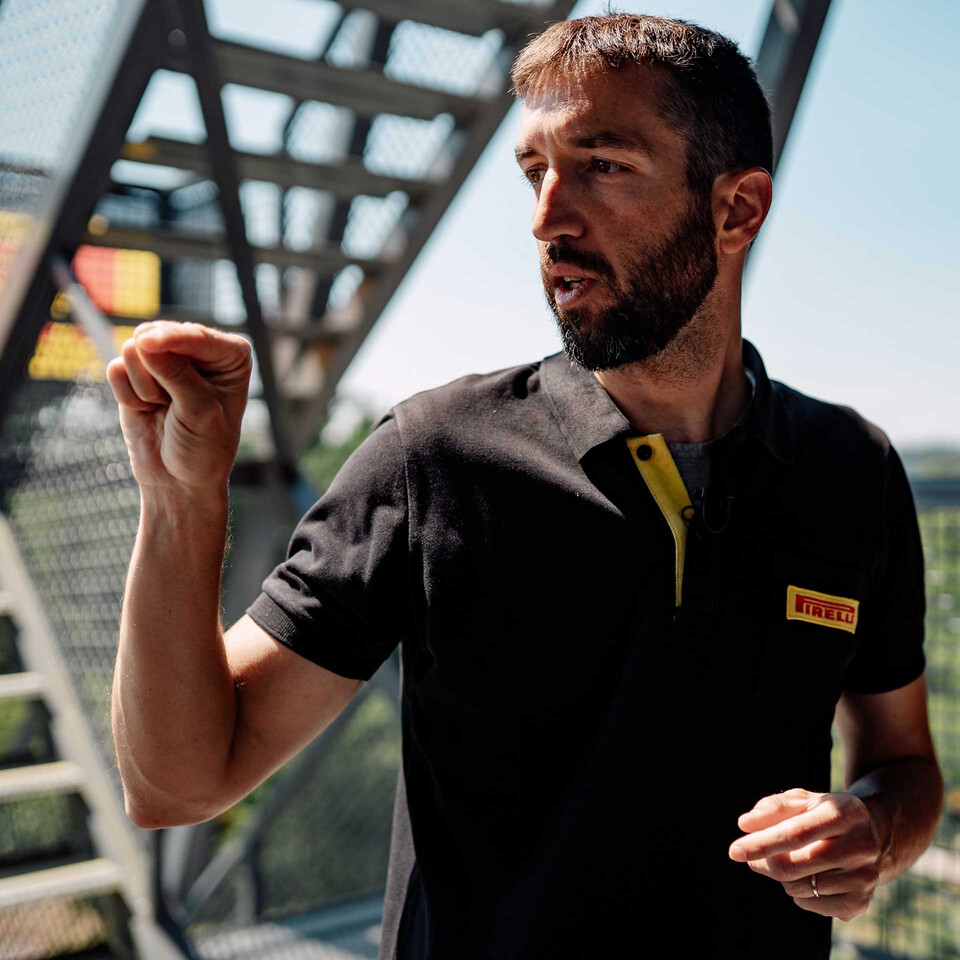
Under the controlled conditions of the wet test track, Pietro Giacoppo puts a set of Pirelli CINTURATO™ road tyres to the test. In the blistering June sunshine, riding through the sprinklers looks surprisingly enviable.
As the test progresses, Product Manager Samuele Bressan explains how aquaplaning is not an issue for road bike tyres, since the contact patch is narrow enough not to require treads to disperse water. “On Pirelli road tyres, the treads are there to provide feedback to the rider. Professional riders need to know at what angle their tyre will fail to keep them upright, and the smoother the transition and more reliable that feedback, the faster the rider can get to that point.”
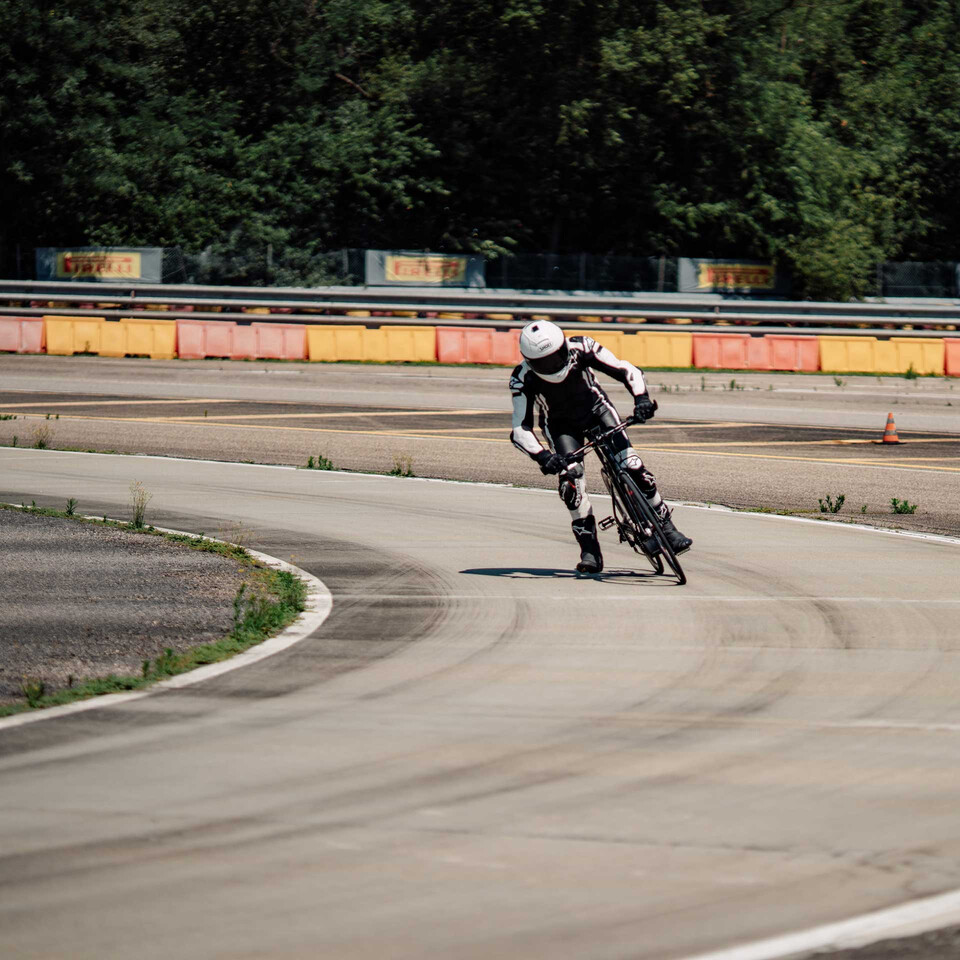
At the centre of the track, a steering pad sits like the face of a watch, with a series of different testable radii offset like a never-ending road. This is where the lean angle of bicycle tyres are tested at a range of speeds, in wet and dry conditions. Here, Pietro rides a modified E-bike with a throttle to keep the speed consistent and avoid pedal strike when leaning deep into the curve. The bike is kitted out with the same sensors the team uses on Superbikes, with GPS systems, an Inertia Measurement Unit and a Data Logger.
With this information, Pirelli knows the cornering limits of their tyres, which is valuable information to pro riders and top amateurs pushing these limits. The feedback of the tyre is also gauged by feel and plotted against these results. By working with UCI WorldTeam Mitchelton Scott, they’ve been able to refine and hone the performance with a focus on predictability in handling.
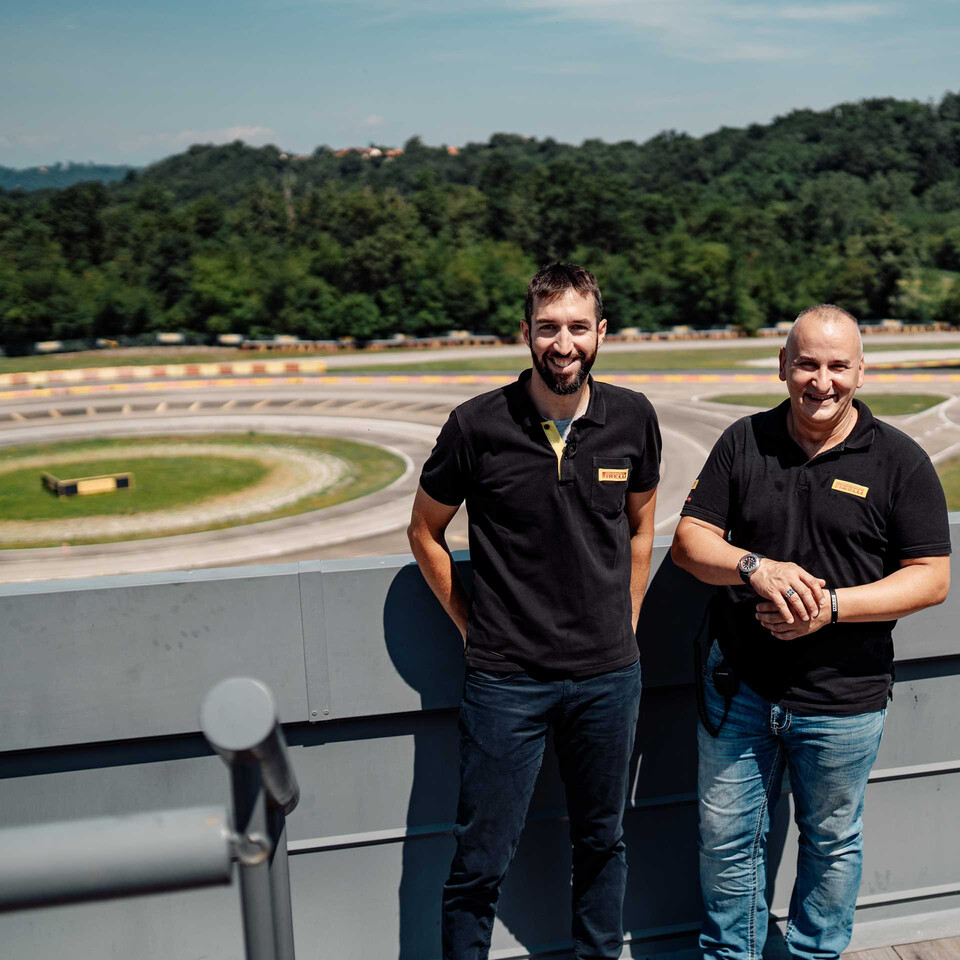
The test track is just one of the various grounds Pirelli uses to develop the grip, mileage and puncture protection of their Velo range. On the Island of Sicily, they have further testing facilities and the benefit of having Mount Etna on their doorstep for testing on challenging real-life descents. On the climb, the tyres are typically tested in a range of temperatures which can reach 40°C at the bottom, while it’s just 10°C at the top. Regular testing includes a standard 135km loop, where two riders will swap wheels midway, to provide a more accurate set of data related to tyre wear.
Arrivederci Pirelli
With the entire Pirelli family all focussed on sharing knowledge and experience, it’s easy to see why this powerhouse’s return to cycling is turning so many heads. By having the same team developing products for all disciplines, a great synergy is created, which is bestowed in all of their tyres.
So the next time you’re deliberating over bike tyres, ask yourself; how many manufacturers truly share your obsession.
Pirelli Velo Range of Bicycle Tyres
